Recognizing Just How a Chemical Defoamer Works to Boost Industrial Processes
Chemical defoamers play a crucial role in enhancing industrial procedures by properly reducing foam-related difficulties. What stays to be explored is just how these defoamers can be tailored to meet particular functional needs.
What Is a Chemical Defoamer?
A chemical defoamer is a material particularly developed to get rid of the formation or reduce of foam in numerous commercial processes. Lathering can conflict with production performance, affecting the quality and performance of products in industries such as food and drink, drugs, and wastewater treatment. Defoamers are important in these applications, as extreme foam can cause operational challenges, such as overflow, lowered blending efficiency, and prevented heat transfer.
The choice of an appropriate defoamer is vital, as various formulations may be customized for specific procedures or kinds of foam. Variables such as compatibility with other components, temperature level security, and the desired application play a considerable role in the performance of a defoamer.
Systems of Defoaming Activity
The systems of defoaming activity include intricate communications between the foam and the defoamer structure. When a defoamer is presented to a frothing system, it migrates swiftly to the surface area of the foam bubbles, displacing the stabilizing representatives that add to foam security.
As smaller bubbles merge into larger ones, the overall stability of the foam decreases. Furthermore, specific defoamers may consist of hydrophobic elements that improve their capacity to destabilize the foam by creating a barrier that prevents bubble development. This dual action-- surface area tension decrease and destabilization-- permits an extra reliable failure of foam.
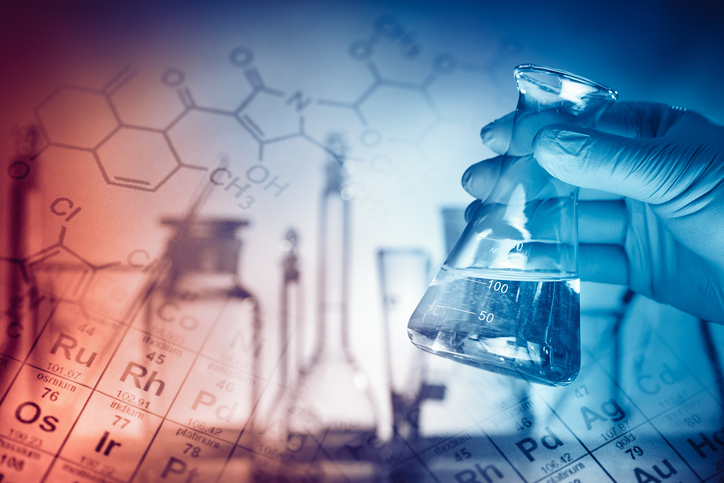
Moreover, the viscosity and dispersing characteristics of the defoamer play crucial roles in its performance. A well-formulated defoamer will make certain rapid migration and optimum efficiency, decreasing foam development throughout industrial processes. By understanding these systems, markets can better pick and use chemical defoamers to improve functional performance and product quality.
Kinds of Chemical Defoamers
Chemical defoamers can be classified right into several kinds, each customized to certain applications and foam difficulties. The main classifications include silicone-based, non-silicone-based, and powder defoamers.
Silicone-based defoamers are extremely efficient due to their capability to spread out quickly throughout fluid surface areas. They provide superb foam reductions and security, making them appropriate for different industrial applications, including finishings and adhesives. Non-silicone-based defoamers, on the other hand, commonly rely upon organic substances like fats or esters. These are especially favored in food and beverage sectors because of their reduced poisoning and governing compliance.
Powder defoamers are composed of solid bits that can be contributed to dry procedures or solutions. They are typically made use of in procedures where liquid defoamers might not work, giving an unique option for specific applications, such as in the production of specific kinds of plastics or powders.
Additionally, each type of defoamer can be tailored with numerous ingredients to boost performance, such as surfactants or emulsifiers, enabling this page flexibility in attending to different foaming scenarios throughout several markets.
Applications in Industrial Processes
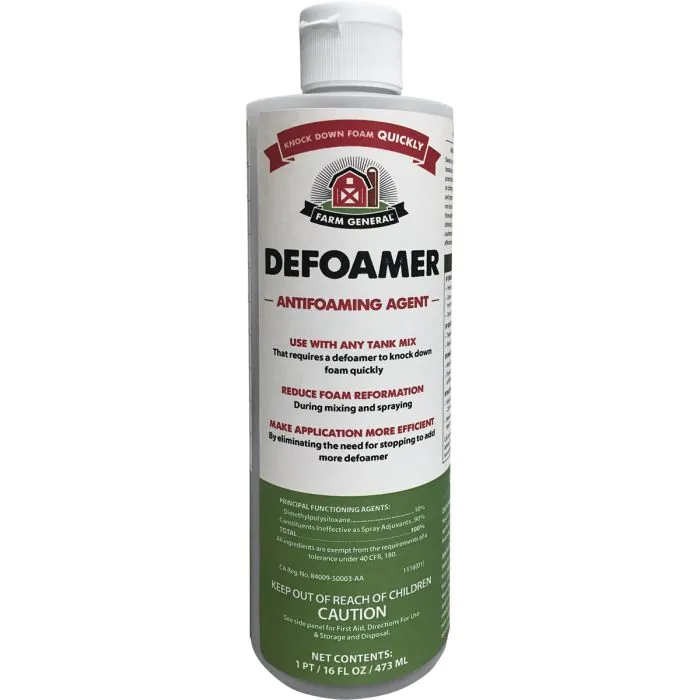
In the food and drink market, defoamers are crucial throughout the manufacturing of juices, beers, and dairy items, where excessive foam can prevent blending and filtering procedures. By minimizing foam development, defoamers aid preserve consistent item quality and maximize processing times.
In drugs, the presence of foam throughout the mixing and solution of medicines can influence dosage precision and product security. Defoamers guarantee smooth procedures, thus promoting the manufacturing of top notch pharmaceuticals.
Wastewater therapy facilities likewise rely on defoamers to control lathering in aeration storage tanks, which can or else decrease therapy efficiency and complicate sludge handling. By effectively taking care of foam, these chemicals enhance the general efficiency of therapy procedures and contribute to governing compliance.

Advantages of Utilizing Defoamers
While foam can provide substantial challenges throughout numerous sectors, making use of defoamers supplies numerous benefits that boost operational effectiveness and product honesty. Defoamers efficiently get rid of or decrease foam formation, bring about smoother manufacturing processes and improved item high quality. This reduction in foam reduces disruptions during manufacturing, enabling constant operation and raised throughput.
Additionally, the application of defoamers can result in cost financial savings by decreasing the demand for excess basic materials and power consumption associated with foam monitoring. By maximizing the production procedure, makers can achieve greater yields and reduced waste, ultimately boosting productivity.
Furthermore, defoamers contribute index to far better devices performance. Foam buildup can bring about blocking, overflow, and tools wear, leading to pricey downtime and maintenance. By avoiding these issues, defoamers extend the life expectancy of equipment and decrease functional costs.
Verdict

A chemical defoamer is a material particularly formulated to remove the development or decrease of foam Chemical Defoamer in numerous commercial procedures. When a defoamer is introduced to a frothing system, it migrates quickly to the surface of the foam bubbles, displacing the supporting representatives that add to foam stability. A well-formulated defoamer will certainly guarantee quick movement and optimal efficiency, reducing foam development during commercial processes. Defoamers properly get rid of or lower foam formation, leading to smoother manufacturing processes and enhanced item quality.In final thought, chemical defoamers play a vital function in improving commercial processes by effectively lowering foam development.